Manufacturing
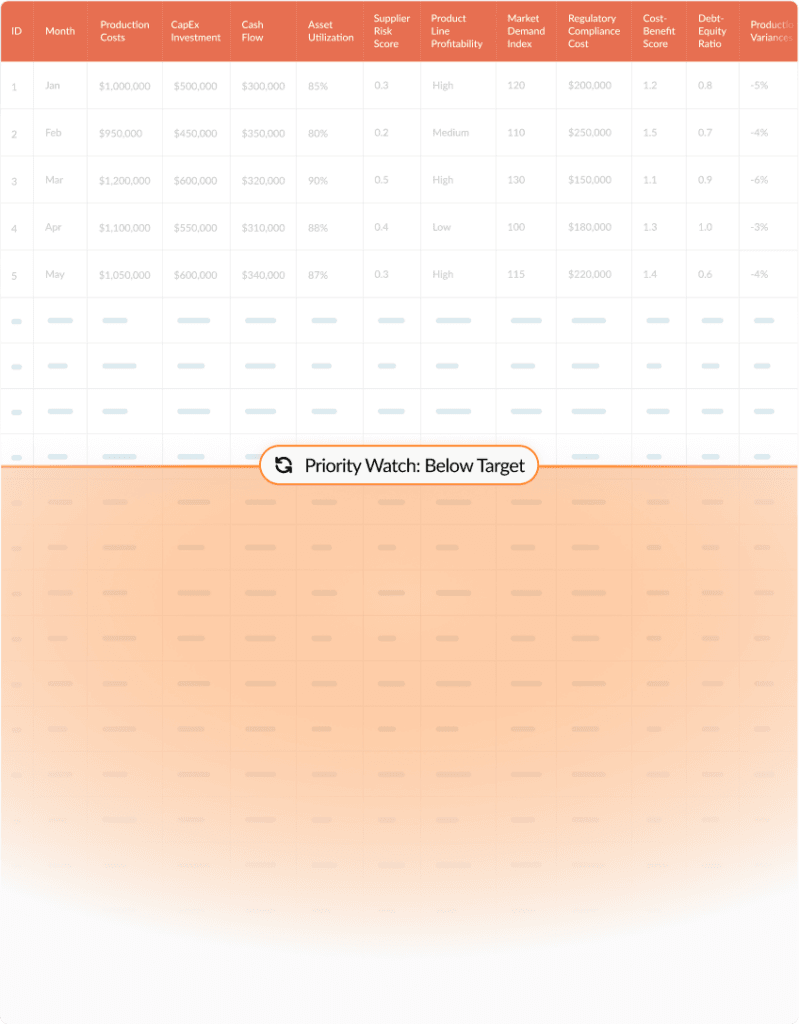
Financial & Capital Analytics
Analyze Production Costs: Scrutinize cost components including raw materials, labor, and overhead to identify areas for cost reduction and efficiency improvement
Evaluate Capital Expenditure (CapEx): Assess the impact of capital investments on production capacity and financial health
Monitor Cash Flow: Track cash flow trends to ensure sufficient liquidity for operational and strategic needs
Asset Utilization: Optimize the use of manufacturing assets by analyzing utilization rates and identifying underperforming equipment or facilities for improvement or divestment
Supplier Portfolio: Balance the supplier portfolio to minimize risks associated with overreliance on a single source and to secure favorable terms through strategic partnerships
Product Line Optimization: Evaluate the profitability of different product lines to focus on high-margin products and consider phasing out underperforming ones
Market Demand Forecasting: Use advanced analytics to forecast demand for manufactured goods based on market trends and consumer preferences
Competitive Analysis: Analyze competitors’ production capabilities, market share, and strategic moves to identify opportunities and threats
Regulatory Impact Analysis: Assess the impact of regulatory changes on manufacturing operations and compliance costs
Cost-Benefit Analysis: Conduct detailed cost-benefit analyses of potential investments in new technologies, facilities, or processes
Scenario Planning: Develop financial models to evaluate the impact of various scenarios such as changes in raw material prices, labor costs, and market demand
Break-Even Analysis: Determine the break-even points for different production levels to support pricing and production planning decisions
Debt vs. Equity Financing: Optimize the capital structure by determining the ideal mix of debt and equity to finance manufacturing expansions and innovations
Capital Budgeting: Evaluate capital projects using methods such as Net Present Value (NPV), Internal Rate of Return (IRR), and Payback Period to prioritize investments
Mergers and Acquisitions: Assess potential acquisition targets for strategic fit and the potential to enhance production capabilities and market reach
Production Variances: Identify and analyze variances in production costs and output compared to budgeted figures, focusing on material usage, labor efficiency, and overhead costs
Sales Variances: Track variances in sales volume and pricing to adjust production schedules and inventory levels
Operational Efficiency: Investigate variances in operational efficiency to identify areas for process improvements and cost savings
Supply Chain Risks: Evaluate risks associated with supply chain disruptions, including supplier reliability and logistics challenges, and develop mitigation strategies
Market Risks: Analyze risks related to market fluctuations, such as changes in demand
Process Mining
Gather data from various stages of the manufacturing process, including supply chain inputs, production line data, quality control logs, and equipment maintenance records
Integrate and synchronize data across different production sites and departments to create a unified view of the manufacturing processes
Build a model of the production workflows for different products, identifying the sequence of operations and the interaction between different machines and human tasks
Evaluate whether the real-world execution of manufacturing processes adheres to planned protocols and quality standards and pinpoint where defects are introduced or where slowdowns occur
Use insights to fine-tune production lines, improve quality control measures, and better schedule maintenance to reduce downtime and increase efficiency
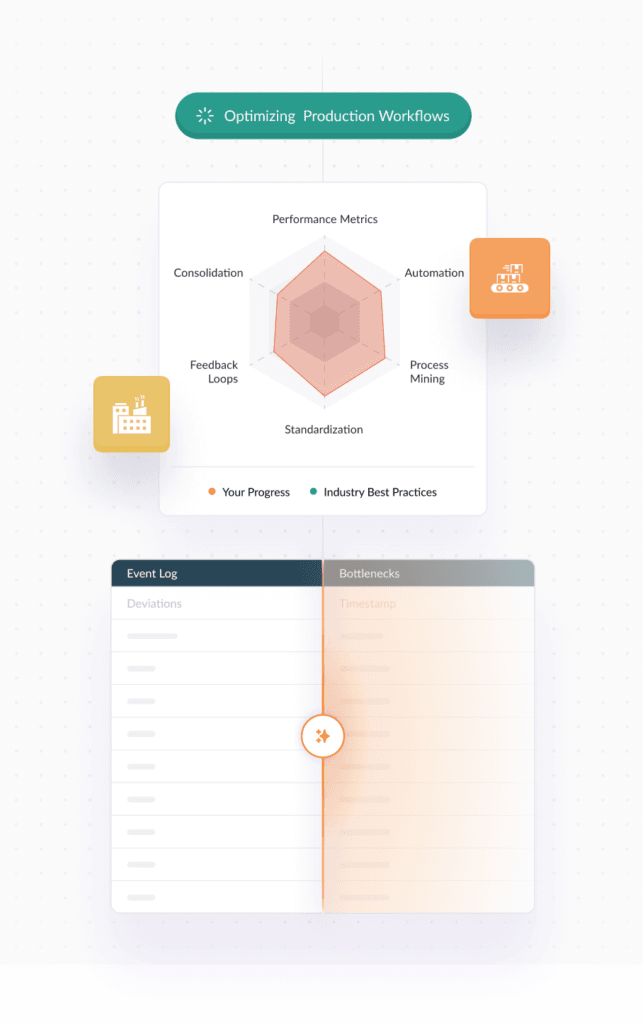
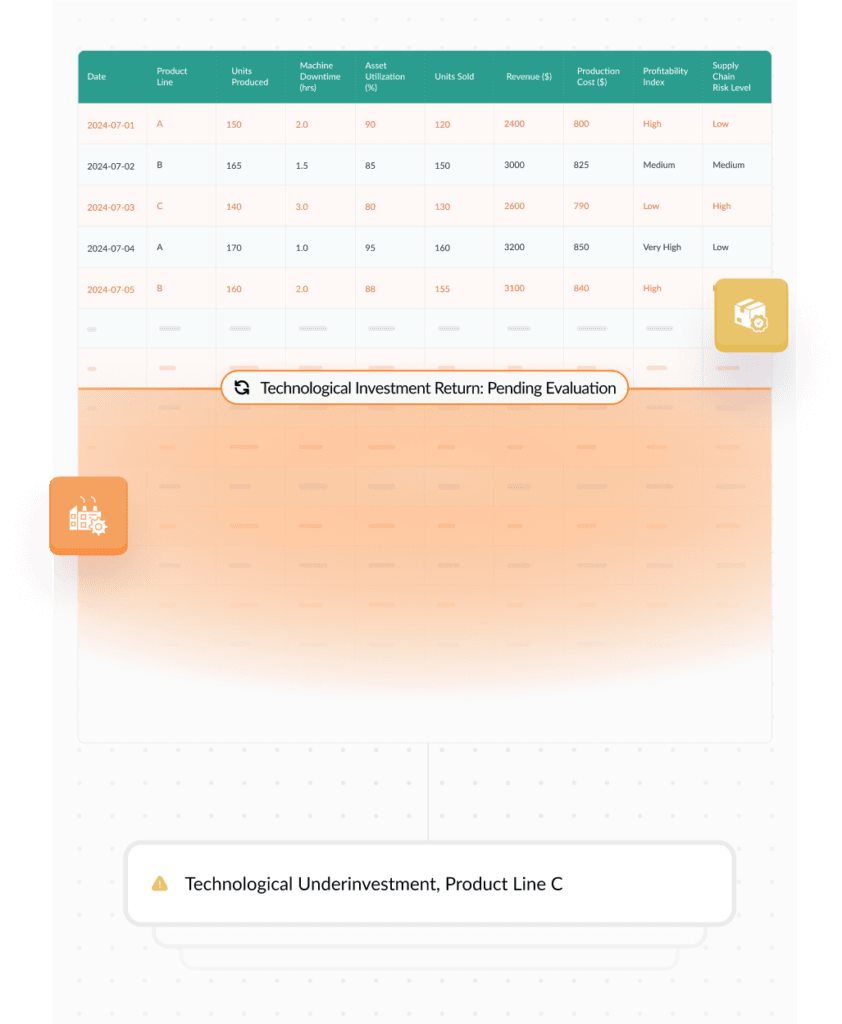
Business Intelligence
Summarize production output and defect rates across different lines to measure overall efficiency and quality control
Analyze machine breakdown incidents to pinpoint common causes, such as specific parts failures or operator errors, by reviewing maintenance records and operational data
Use machine learning models to predict equipment failures and downtime by analyzing patterns from historical sensor data and maintenance logs
Recommend maintenance schedules or adjustments in machine settings to minimize downtime and improve production efficiency based on predictive analytics findings
Integrate data from production metrics, quality control, and market feedback to infer the relationships between manufacturing processes and product quality, guiding future improvements
Streamlining
In this section, we outline industry-specific profiles to showcase how streamlining efforts can enhance operational efficiency and reduce costs across different manufacturing contexts. By mapping production steps and identifying inefficiencies, we provide targeted solutions that align with the unique needs and challenges of each sector
Map out customer service processes, inventory management, order fulfillment, and returns processing can highlight inefficiencies such as slow-moving inventory or redundant steps in customer service
Automate repetitive tasks like stock ordering, pricing updates, and customer inquiries through CRM systems, automated re-ordering systems, and AI models, which can significantly streamline operations
Implement systems to track sales performance, customer satisfaction scores, and inventory turnover rates. Using KPIs like Average Handling Time (AHT) and Net Promoter Score (NPS) can help measure the effectiveness of sales strategies and customer service
Reduce layers of management by merging similar departments like customer service for online and offline channels. Combining procurement for different categories can also reduce costs and simplify supply chain management
Create uniform processes for handling customer queries, returns, and pricing across all stores and e-commerce platforms to ensure a consistent customer experience and easier management
Collect feedback from customers through surveys and feedback forms online and in-store. Employee feedback on the retail floor can also provide valuable insights into operational improvements
Assess the impact of streamlining efforts on sales growth, customer satisfaction, and operational costs. Adjust strategies as needed to ensure continued improvement
Map every step of the production line using data visualization tools like to identify inefficiencies and optimize workflows
Automate repetitive tasks with data-driven decision systems that analyze tasks suitable for robotics to improve precision and reduce labor costs
Get benchmarks for success by implementing ERP systems that provide real-time data on production metrics, allowing for informed operational decisions
Reduce layers of management and combine similar processes by using data analytics to evaluate the impact of integrating multiple production facilities or streamlining management structures
Standardize the use of common parts across different models using data analyses to minimize inventory complexities and reduce costs
Stay responsive to changing needs by deploying real-time data collection tools that enable frontline workers to report issues via mobile apps or IoT devices
Pause periodically to review data on technological upgrades and their impacts on production efficiency and waste reduction
Visualize and refine workflows in PCB (Printed Circuit Boards) assembly using data visualization tools to help identify and correct inefficiencies
Speed up production with automated solutions informed by data analyses that identify bottlenecks and inefficiencies
Detect anomalies in real-time production data using data integration and analytics tools to improve quality control
Merge similar product lines by analyzing shared resource utilization with data analytics, improving efficiency
Create standardized design templates based on data analysis to ensure compatibility and interchangeability across components
Gather and analyze customer feedback for product improvement using data aggregation platforms to improve product quality and customer satisfaction
Evaluate the impacts of automation and process improvements by analyzing data on cycle times and yield rates to make informed adjustments
Reduce material waste in processes such as dyeing, weaving, and finishing by using statistical tools for detailed data analysis
Introduce automated systems in fabric cutting, informed by data analytics that pinpoint inefficiencies and accuracy issues
Track fabric usage and production speed efficiently using ERP solutions to streamline operations
Combine fabric treatment operations based on data analyses, which consolidate processes and optimize resource use
Harmonize dye formulas using data-driven methods to ensure consistent color quality across batches
Collect and analyze data on operator interactions with machinery settings and material handling to improve process controls and feedback mechanisms
Assess the impact of new technologies and practices on sustainability and efficiency by conducting data periodic reviews
Visualize and optimize workflows using data visualization tools to identify inefficiencies and bottlenecks in machining and assembly lines
Analyze operational data to identify processes suitable for automation and improve efficiency through predictive analytics
Monitor machine efficiency and maintenance needs using data analytics platforms to predict failures and schedule proactive maintenance
Consolidate multiple small assembly lines using data-driven insights to reduce overhead and improve operational efficiency
Standardize processes and components based on data analysis to reduce production complexity and streamline inventory management
Implement feedback systems using data collection tools to gather and analyze operational data from machinery to inform continuous improvement strategies
Evaluate the impact of implemented lean manufacturing principles through data reviews to identify successful strategies and areas needing improvement
Simulate chemical processes using data modeling tools to predict bottlenecks and optimize flow rates and mixing processes
Deploy data analytics to optimize the timing and dosage of chemical feeds, thereby reducing variability and improving yield
Track reactant efficiencies and waste levels using data integration tools to enhance resource management and reduce costs
Merge similar production lines based on analysis of operational data, enhancing overall efficiency and reducing waste
Harmonize safety and handling protocols across facilities using data-driven policy standardization to ensure consistency and regulatory compliance
Establish incident reporting and response systems based on real-time data collection to quickly address safety and operational issues
Review data on environmental impacts and regulatory compliance to gauge the efficiency of process changes and maintain adherence to environmental standards
Map out production processes using process flow mapping software to visualize and eliminate inefficiencies from raw material receipt to final packaging
Utilize machine learning to optimize automation of filling and packaging processes, enhancing speed and reducing contamination risks
Track product quality metrics such as consistency and spoilage using ERP systems to manage production more effectively
Analyze logistics and production data to identify opportunities for consolidating production lines and reducing costs
Standardize recipes and ingredient sourcing across facilities using data analysis to ensure product uniformity and streamline operations
Create consumer feedback analysis tools to systematically gather and respond to customer inputs, thereby improving product quality and satisfaction
Conduct data-driven audits to verify the efficiency of production technologies and adherence to standards, fostering continuous improvement
Analyze the entire device fabrication process from design to assembly using data analytics to ensure standards compliance and minimize errors
Implement automated assembly systems based on data insights to improve precision and reduce manufacturing costs
Monitor key performance metrics like yield and rejection rates using data analytics to maintain high-quality output and efficient production
Merge quality assurance processes informed by data analysis to optimize testing without compromising safety
Adopt uniform designs and materials based on analytical studies to streamline regulatory approvals and reduce production timelines
Facilitate communication between R&D and production using data-sharing platforms to quickly adapt to regulatory changes and incorporate new technologies
Pause periodically to review data on process improvements to evaluate their impact on device reliability and production efficiency
Diagram each step of the design and production process using process flow mapping software like Lucidchart to identify wasteful activities and optimize material usage
Analyze operational data to identify tasks suitable for robotic automation, facilitating precision and reducing waste
Measure key metrics such as material utilization rates and on-time delivery performance using ERP systems like Oracle or SAP
Combine similar manufacturing workshops based on data analysis to reduce costs and improve logistical efficiency
Enforce uniform quality standards and production procedures across all product lines through data-driven policy standardization
Establish digital feedback mechanisms for customer and employee inputs to continuously improve product designs and customer satisfaction
Assess the effectiveness of new machinery and design software on product quality and production times by analyzing performance data
Examine each phase of paper production, from pulp processing to final rolling, using data visualization tools to streamline operations and reduce energy consumption
Deploy data analytics to optimize the automation of paper machine adjustments for thickness and moisture content, thus enhancing production speed and reducing waste
Observe performance indicators such as energy usage and production efficiency using integrated management software to identify improvement areas
Integrate smaller production units into larger facilities based on data-driven assessments to enhance economies of scale and comply with environmental regulations
Implement standardized procedures for quality control and maintenance across all plants using data analysis to ensure consistent product quality
Develop feedback systems that use data collection tools to gather insights from operators on machine efficiency and paper quality, enabling immediate adjustments
Reflect on the environmental and financial impacts of process optimizations and sustainability initiatives through regular data reviews
Chart all processes from raw material handling to final product finishing using process analysis tools like Microsoft Power BI to pinpoint inefficiencies and potential improvements
Introduce data-driven decision-making to implement robotic systems for tasks such as welding and materials handling, increasing production speeds and reducing labor costs
Monitor critical metrics such as alloy composition and temperature control during smelting using specialized data analysis software to ensure product quality
Simplify production by analyzing data to combine operations that can share the same equipment and workforce, reducing operational complexities
Regulate manufacturing processes through data-driven standardization to ensure a uniform approach in handling and processing different metals, which simplifies training and improves safety
Organize continuous improvement meetings that use data collection and analytics to gather feedback from the shop floor and adjust processes in real time
Verify the benefits of investments in new technologies and process changes by conducting thorough data reviews of production and financial records
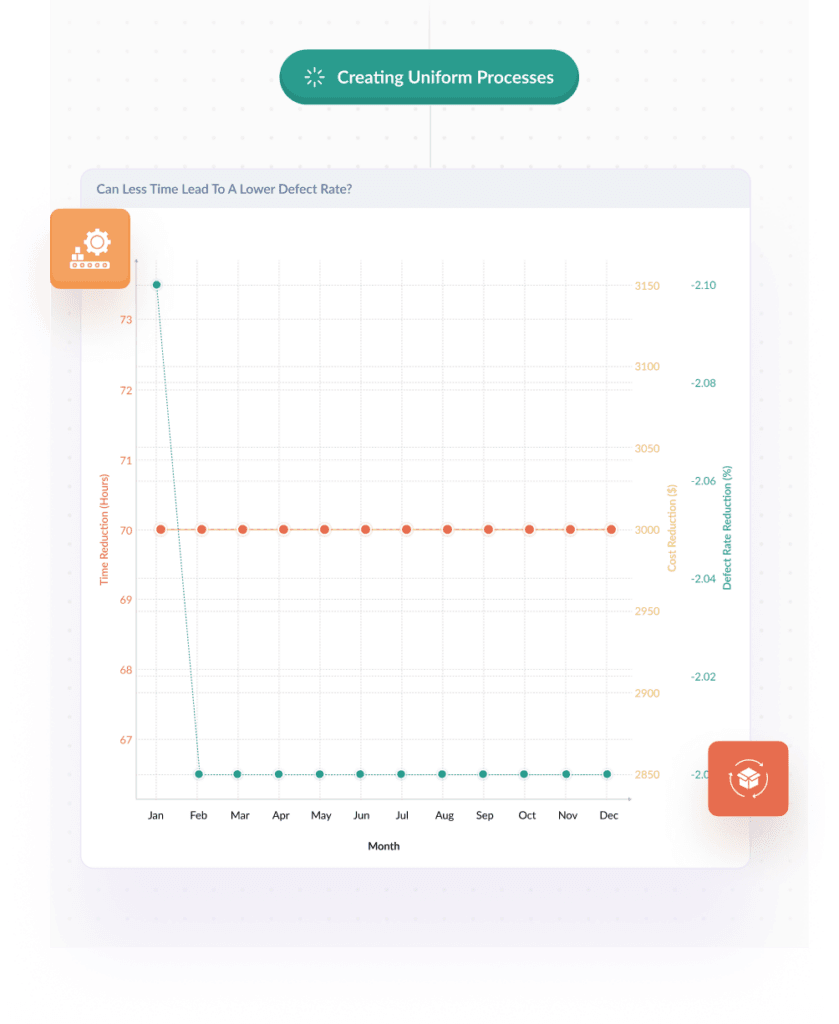